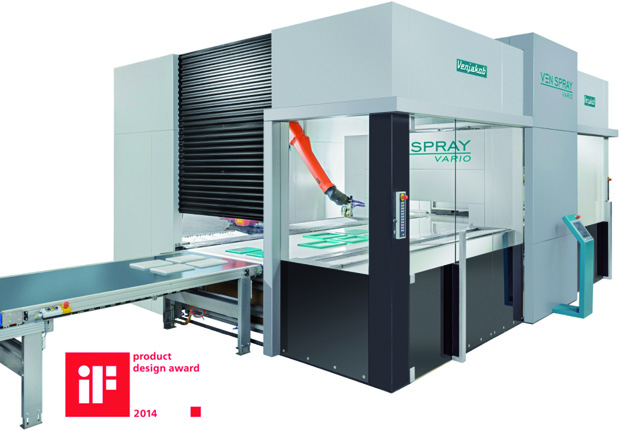
Wie Lackieranlagen durch intelligente Funktionen künftig leistungsfähiger werden, erarbeiten aktuell Wissenschaftler des Heinz Nixdorf Instituts (Universität Paderborn) in Zusammenarbeit mit dem Lackieranlagenhersteller „Venjakob Maschinenbau“.
Eine Lackieranlage, die frühzeitig den Verschleiß von Bauteilen erkennt und dies über ein Display dem Anlagenbediener meldet – über solche Funktionen könnten intelligente Lackieranlagen zukünftig verfügen. Im Rahmen des Transferprojekts „ISOLack“ hat das Forscherteam um Prof. Dr.-Ing. Jürgen Gausemeier untersucht, wie Lackieranlagen verbessert werden können. Dafür ermittelten die Wissenschaftler, wo Verbesserungsbedarf besteht und wie diese Verbesserungen umgesetzt werden können. Im Anschluss daran hat das Team zusammen mit „Venjakob Maschinenbau“ Nutzen und Aufwand abgewogen, um festzustellen, welche intelligenten Funktionen in den Lackieranlagen der Zukunft integriert werden sollen.
Lackieranlagen sind etwa 30 – 40 Meter lange Maschinenstraßen. Wird ein Werkstück lackiert, durchläuft es die Anlage und wird verschiedenen Prozessen unterzogen. Das Werkstück wird zuerst gereinigt, dann vorbehandelt, lackiert und getrocknet. „Wir haben unter anderem überprüft, wie der Reinigungsprozess optimiert werden kann“, erklärt Dipl.-Ing. Peter Iwanek, der an dem Projekt mitgearbeitet hat. Bei der Reinigung neutralisiert ein Ionisierstab geladene Staubkörner auf dem Werkstück und ermöglicht die Entfernung dieser. Ein Luftprofil mit entsprechender Druckluft vervollständigt den Reinigungsprozess. „Wenn die Leistung des Ionisierstabs nachlässt und die Wartung nicht rechtzeitig erfolgt, hat das Auswirkungen auf die ganze Produktion“, so Iwanek. Denn befindet sich beim Lackiervorgang noch Staub auf dem Werkstück, entstehen Unebenheiten und das Werkstück wird unbrauchbar. Um solche Störungen in Zukunft zu verhindern, haben die Wissenschaftler zum Beispiel das Potential identifiziert, maschinelles Lernen zur vorausschauenden Wartungsplanung einzusetzen (Condition Monitoring). „Hierdurch soll die Lackieranlage dem Anlagenbediener auf einem Display anzeigen, dass das Bauteil in Zukunft gewartet werden muss“, erläutert Iwanek.
Das Transferprojekt „ISOLack“ („Identifikation von Potentialen der Selbstoptimierung im Bereich der Oberflächenlackierung) begann im Oktober 2014 und wurde im Rahmen des Spitzenclusters „it’s OWL“ vom Bundeministerium für Bildung und Forschung gefördert